Prellis Biologics, Inc. has developed an intuitive web-based interface tailored for biologists and tissue engineers that can be learned in minute
This press release features multimedia. View the full release here: https://www.businesswire.com/news/home/20191210005837/en/
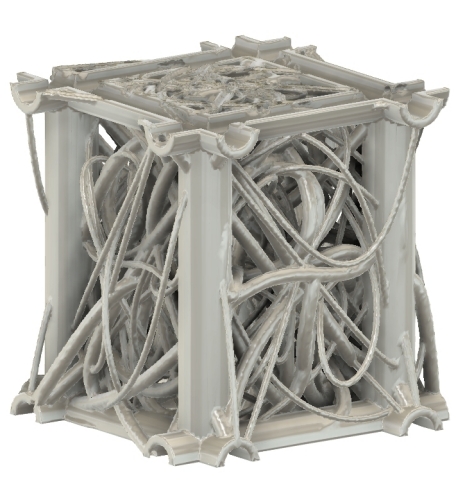
This is a rendering of the "Dense Curves" 3D scaffold offered by Prellis Biologics and designed with its new TissueWorkshop™ web-based interface tailored for biologists and tissue engineers. The structure is 1 cubic centimeter, framed by large 1000 micron (1mm) channels. the interior of the structure is a dense packing of fifty 100 micron curved tubes. All channels are hollow with 100 micron thick walls, allowing for sufficient cellular nutrient and waste exchange. The scaffold represents an unbiased approach to three-dimensional architecture (curvature and angling) for optimizing 3D cell culture. (Photo: Business Wire)
“Every day I saw my expert team toiling away designing CAD files by hand. The time it took to design a single file is prohibitive for us to quickly answer relevant 3D tissue engineering questions,” said Prellis Biologics’ CEO Melanie Matheu, PhD.
“We had to move the bar on iteration time. We’re the first team in the world that can begin to ask the question of which high-resolution scaffold is best for building a liver or piece of cartilage. I didn’t want my team spending decades of human-powered design time to do so,” she said.
TissueWorkshop™ was built with tools and principles used in video game development and 3D animation. Gavan Wilhite, founder of AltspaceVR, developed this novel approach to human tissue engineering specifically with biologists and tissue engineers in mind.
“The gaming industry has poured tremendous resources into tools that are often unfamiliar to those outside the sector. It’s a special joy to use them to accelerate the positive impact that tissue engineering has to offer,” said Wilhite.
Tailored for biologists and tissue engineers, the software is an intuitive design system that can be learned in minutes, while many standard CAD software programs require multiple university level classes that are not typically part of the biological scientist’s curriculum.
TissueWorkshop™ allows users to build CAD files that match most 3D printer resolutions of 50 and 100 microns, allowing printing of structures on extrusion bioprinters such as the BIO X6 from CELLINK, Inc.
“The BIO X6 gives the user freedom to combine multiple materials in one print and the capability to create more complex architectures,” said Itedale Namro Redwan, CSO, CELLINK. ”Being able to use different pressures, temperatures and printing methods simultaneously in six different positions is revolutionary, providing the cells with the biological environment they need to achieve the desired architecture,” she said.
“Finding the best architecture has been incredibly challenging due to the inability to scan potential 3D structures in an unbiased way with available CAD programs,” says Erin Stephens, PhD, Director of Tissue Engineering at Prellis. “It would simply take too long.”
TissueWorkshop™ is also available to build structures at the 1-micron resolution for owners of the Holograph-X system sold by CELLINK, Inc.
“The Holograph-X Bioprinter enables in-lab manufacturing of capillary-containing organ structures and tissues for transplantation, therapeutics screening and complex 3D culture development,” said Erik Gatenholm, CEO, CELLINK. ”We’ve combined key strengths of our two companies, resulting in cutting edge technology for our partners and customers and empowering them to advance their research in the field of 3D-bioprinting of human organs.”
The Prellis Team has released ten tissue scaffolds produced by TissueWorkshop™ that can be printed at the 100 micron resolution on the BIO X6 or any 3D printer of 100 micron resolution. Ten tissue test structures can be downloaded today from the Prellis Biologics website: www.prellisbio.com/tissueworkshop.
Prellis Biologics is currently beta testing with select users (sign up here: info@PrellisBio.com) and launching an open beta of TissueWorkshop™ January 15th 2020.
About Prellis Biologics, Inc.
Prellis Biologics, Inc. developed the first holographic printing system able to match and accurately replicate human organ and tissue structures for R&D and organ transplantation. The combined resolution and speed of Prellis Biologics’ printing technology allows for full human organ systems to be created with cell-compatible biomatrices. We are dedicated to solving the global human organ transplant shortage. Prellis Biologics, Inc. was founded in 2016 and is a privately held company based in San Francisco, CA.
More information on Prellis Biologics can be found here.
View source version on businesswire.com: https://www.businesswire.com/news/home/20191210005837/en/
Contacts
Krause Taylor Associates for Prellis Biologics, Inc.
Barbara Krause
408.981.2429
barbara@krause-taylor.com
Source: Prellis Biologics, Inc.
Smart Multimedia Gallery
This is a rendering of the "Dense Curves" 3D scaffold offered by Prellis Biologics and designed with its new TissueWorkshop™ web-based interface tailored for biologists and tissue engineers. The structure is 1 cubic centimeter, framed by large 1000 micron (1mm) channels. the interior of the structure is a dense packing of fifty 100 micron curved tubes. All channels are hollow with 100 micron thick walls, allowing for sufficient cellular nutrient and waste exchange. The scaffold represents an unbiased approach to three-dimensional architecture (curvature and angling) for optimizing 3D cell culture. (Photo: Business Wire)
This is a rendering of the "Basic Dense" 3D scaffold offered by Prellis Biologics and designed with its new TissueWorkshop™ web-based interface tailored for biologists and tissue engineers. The structure is 1 cubic centimeter, with 200 and 500 micron channels randomly distributed throughout the horizontal and vertical planes, meeting at 45 and 90 degree intersections respectively. The scaffold was designed to maximize surface area and packing density of hollow tubes, facilitating dense cell seedings while allowing for adequate oxygenation. (Photo: Business Wire)